Early watch movements with verge escapements didn’t have jewel bearings, so it was simply metal on metal that resulted in a lot of friction and wear. Of course, arbors today are set in synthetic jewel bearings, but it wasn’t until the 20th century that this technology was used. That doesn’t mean that watches prior to this had archaic movements without bearings, but they used natural jewels that were much more expensive and harder to work with. In fact, natural jewel bearings have been used in watchmaking since 1704, so efficient and (relatively) accurate timepieces have been around for well over three centuries.
Early 18th Century
Nicolas Fatio de Duillier, Peter Debaufre, and Jacob Debaufre were the first to use natural jewel bearings in 1704 and received a patent for the concept. Jewels were usually rubies, garnets, sapphires and even diamonds (a favorite of Breguet), formed largely by hand with fairly basic tools. These provided hard and resilient surfaces that were also slick and very wear resistant for metal arbors attached to gears and other critical points. Friction was greatly reduced and the need for lubricants lessoned, allowing movements to run more efficiently and accurately. Maintenance was also improved as bearings significantly decreased wear, improving longevity and reliability. Additional benefits of jewel bearings are stability during temperature fluctuations and corrosion resistance, although they’re also brittle and work best in small applications like watch movements.
Jewel Alternatives
One of the best known watchmakers to use alternative materials for movement bearings is Timex. To reduce costs and retail prices, the brand adopted Armalloy in the mid-20th century, which was a hardened alloy developed for missile bearings (among other things) during World War 2. These alloy bearings proved to be adequate alternatives for movements and were both cheaper and easier to produce. Timex punched out inexpensive Armalloy movements by the millions with the help of efficient manufacturing (developed while making wartime precision timers for bomb fuses), automation and simplicity of design. Although Armalloy bearings resisted wear and handled lubrication very well, they were more temperature sensitive and still less durable than jewels, limiting their use to cheaper watches for the masses. This was perfect for Timex, but less ideal for traditional Swiss watchmakers who wouldn’t compromise design, accuracy and longevity with alloy bearings.
Synthetic Jewels
Two centuries after the use of natural jewels in watches, Auguste Verneuil invented the process to make synthetic sapphires and rubies (corundum) in 1902 for watch movements. The first synthetic rubies, however, were made in 1837 by Marc Antoine Gaudin, but it was Verneuil’s flame fusion process that allowed production on a commercial scale for watchmaking. Prior to this, natural jewels were formed via diamond abrasives and grinding, but lasers, ultrasonic milling and chemical etching are used for modern synthetic jewels, increasing production capacity and reducing costs. Synthetic jewels aren’t considered precious stones like their natural counterparts, although they remain more expensive than hardened alloys. A typical synthetic jewel is generally one step below a diamond in hardness.
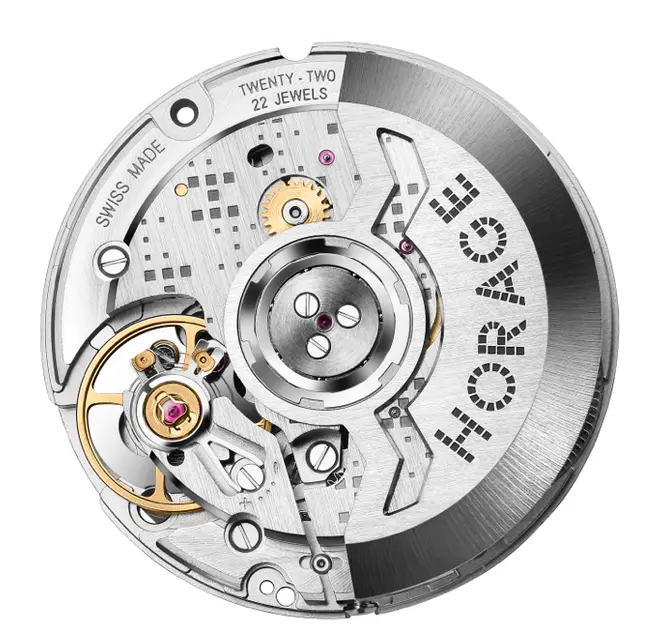
Beyond Bearings
Synthetic jewels aren’t just used as bearings in movements. The pallet fork in conventional escapements have a jewel at the end of each arm that engage with the escape wheel, reducing friction and wear as it contacts the wheel’s teeth. This is vital for efficient performance of the escapement, but materials like silicon reduce friction even more. Among the most efficient and durable escapements are those made from silicon (wheel and anchor), which don't require jewels on the pallet fork as the silicon material itself is incredibly friction and wear resistant. This is exactly what’s used in all of our movements - K1 automatic, K2 micro-rotor and K-TOU tourbillon. Our recent addition of a silicon hairspring improves efficiency and performance even more.
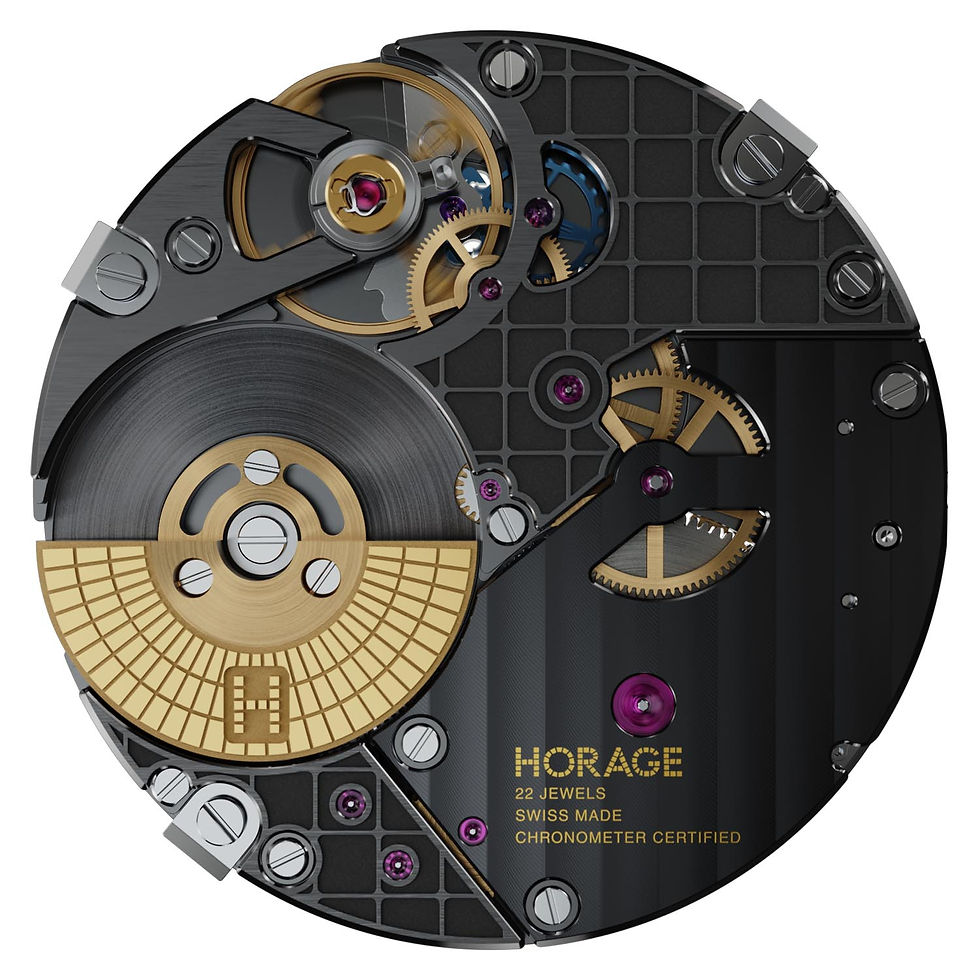
A Fully Jeweled Movement
A time-only movement is considered “fully jeweled” with 17 jewels in total - two pivot jewels in the escape wheel, second, third and fourth wheels, two pivot jewels for the pallet fork along with two pallet jewels for the arms (to engage with the escape wheel), two pivot jewels and an additional impulse jewel for the balance wheel, and two cap jewels. Complications require additional jewels, but an arbitrary increase of jewels usually doesn’t equate to a better movement. High jewel counts are sometimes marketing tools for spec sheets, but less jewels often mean that a design is streamlined and optimized. Cap jewels are used by high-end watchmakers for additional shock resistance, usually stacked with a pivot jewel. This can bring the jewel count of a fully jeweled movement from 17 to 21 (or more). Our K-TOU tourbillon has 19 jewels, while the K1 automatic has 22 jewels and the K2 micro-rotor 25 jewels (both with additional complications).
Horage, Jewels and Silicon
The jewels in our K1 automatic, K2 micro-rotor and K-TOU tourbillon are again used when pressure between the pin of a gear and the resting plate exists and the surface pressure can be calculated. Depending on the pressure and other factors, a decision is made if a jewel is needed. We use the most efficient designs and optimal jewel count for all of our movements, and a chronometer level of accuracy across the board is a testament to our in-house engineering.
Our silicon escapements are as efficient as they come, requiring just a strategic placement of oil. Friction and wear resistance are so optimal with silicon that it again forgoes the need of pallet fork jewels. This results in a lighter, more efficient package.

We Want to Hear From You!
Sound off in the comments about additional topics of interest, so we can be sure to cover what you want to read in future articles. And please share this with friends and anyone interested in watchmaking, and let's keep the conversation going. Also, be sure to sign up for our newsletter (here) and keep an eye out for new products as we're always in the process of development. Check out journal entries as well (here) and a detailed section on performance watchmaking at Horage (here).
We'll talk again soon!
Erik Slaven
Is there any work/engineering ongoing to make more of the gear train from silicon. Would seem if it works for the escape wheel the train of gears would be another implementation. It seems like it might be cheaper and more precise in production, once initial engineering is completed, as well as offering a less friction interface between gears.
Very informative and makes me appreciate even more the K2 movement in my upcoming Supercede!