Lockdown, Breakups & Resurrection.
2020 was an incredibly challenging year for everyone around the world and our team at Horage was of no exception. We had started that year positive with a tourbillon in our hands and the first pre-order underway. At that time we were still even more so unknown than we are now so every watch sold was incredibly important to our development, more so than we would realize, as in March 2020 Switzerland and the world would go into lockdown.

The plan from March 2020 onward was to do a lot of traveling hosting events around the world, however on March 16th it became clear that life as we knew it would change. On March 17th I updated the community with the news that we would have to postpone our events. On the positive side this initiated our move to create more video and start with dipping our toe into the realm of live shows via instagram.
The forum update on that March 17th was void and still void of a comment as most I believe were still trying to digest what was happening in the world. I had hoped it would just be a month or so, but that turned into a couple of years.

Andi catching the train in Taipei shortly before the world went quiet. Check the forum post here.
We closed off the first pre-order round at the end of March with plans of a second pre-order in May. Unfortunately things globally started to worsen and our hopes of getting out and showing watches evaporated. The Swiss watch industry as a whole was cutting production, staff and preparing for an early summer vacation with no end in sight. There was little optimism for a positive outcome and this was causing some very unpredictable behaviour.

Always with a positive attitude in good times and bad Andi knows how to find a way to make the most of things .
A Change in Management
We were shocked to learn that Florian Serex would be leaving his position as CEO at La Joux Perret (LJP). Jonas and our team continued to push forward with requests for the modification required on the movement. With a new CEO in place at LJP the request for movement modifications would fall on deaf ears and the terms of our agreement would not be honoured. From one day to the next the relationship was terminated.
With pre-orders in hand from customers we had two choices. Either throw in the towel and refund all orders or take on the impossible and develop the movement ourselves.
Heated debates would be an understatement to what was going on behind the scenes at Horage. We had the K2 micro-rotor in development and now there was the absolutely insane idea that we needed to create a tourbillon.
Now, anything is possible with right team, enough time and liquid funds on hand, but this was happening amidst a global pandemic. Brands in all directions were closing the doors for the year, suppliers were wondering if they could survive the year with production orders being cut and here we were with around 70 orders on hand, needing to create a movement on next to no budget and in just six months time (later to be eight months).
Watch the video and check the forum post here
Andi and Tzuyu have an uncanny ability to face the most uncertain of moments head on and not back down. The decision was made to literally put the house and all assets of the company on the line to go all in on developing the tourbillon. Where others were laying off staff and closing doors we doubled down on engineering and development. Florian was now a free agent and he joined the team. Silvan worked side by side with Florian as he would later take the reigns and become the production lead on Tourbillon 1. Pascal would step up and work directly with Jonas on K2 to ensure it kept moving forward. Markus would also join Horage as an engineer and take on the responsibility of engineering the tourbillon cage. Leon would step in as a relief watchmaker helping Lenny and Marcella with decoration, regulation and quality control.
What Did We Get Ourselves & You Into?
The news of taking on the movement development entirely on our own was met with both words of overwhelming support, disbelief, encouragement and of course disappointment and anger. On the upside it was primarily all positive, but there were still many emails and phone conversations to discuss in more detail. We understood that emotions were already high with everything happening globally and that some were legitimately concerned that the rug might be pulled out from under them. Although we have always operated on shoe string budgets we have always been transparent and managed to deliver on past projects. Tourbillon 1 was proving to test and push us to the next level of commitment.
With the LJP prototype we hoped to finish movements in September and deliver in October 2020. We optimistically communicated that we would need around three additional months to complete the movement. At that rate we would have a movement complete sometime in January 2021. To put things in perspective a ground up movement development takes years and not definitely not months to achieve. This timeline to our knowledge had never been achieved in movement development, let alone amidst a global pandemic.
Andi and myself got to work on communication and began to make our first video updates on the processes involved.
How was it made possible?
The positive side to the pandemic is that our team understood the seriousness of the situation and were laser focused on the challenge. Every supplier in the watch industry was without orders and we were the crazy ones coming to them with a new project. Normally scheduling a new part with a supplier for production takes months to upwards of a year. After going into production the first samples still need to be tested and often times multiple times before going into series production. In the summer of 2020 it was a different story, our suppliers and us had something exciting to work on amongst a very grim outlook in the market. There were zero wait times and we could take a drawing directly in to be produced, then tested and then back out again to series production.
Regardless of the importance or size of parts, each and every one of the 101 part count in Tourbillon 1 is stringently quality controlled.
We had also put all the parts and components we had development for both K1 and K2 on the table to see what we had to work with and what was still left to develop. Luckily we had already de-risked K1 and much of K2 by that time and we began utilizing parts and sub-assemblies to create the framework. Given that we were working with all our own parts our next challenge was seeing how close we could get to the original aesthetic of the watch that was already pre-ordered. Given the semi-skeletonized design we started the "opening and closing" exercise as I like to call it as the window cutouts in the main plate and bridges would need to change to accommodate the positioning of our architecture.
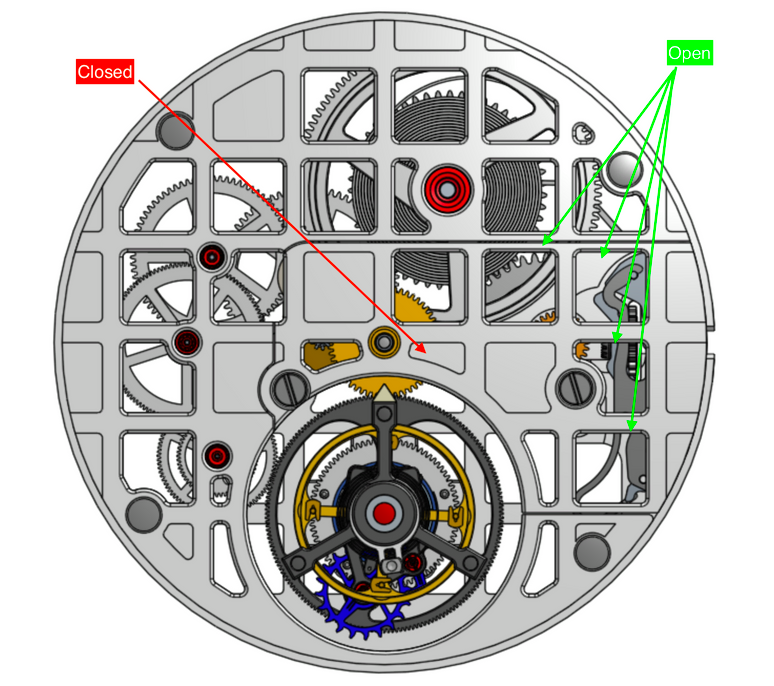

You will notice that the jewel count also changed. Adding and subtracting friction points creates fluctuations in the jewel count. Many changes would be made to get to where things needed to be.
In addition we were making a completely new tourbillon cage based on a bearing construction to increase stability and longevity of the movement. Markus and Andi both coming from the cycling industry have a lot of knowledge and experience with bearings and based the cage construction on this. With a new cage we could also meet customer requests of a seconds indicator. Again since this was a completely new cage we had freedom to do what Jonas set out to do at the inception of the project and that was make the cage and movement the absolute best we could.

A render of the tourbillon cage. Eventually it would have a rhodium (silver optic) screw balance wheel as well as the wheel bridge dimensions increase by 0.2mm in thickness to ensure greater stability.
The cage would become one of the lightest in the world at 0.29 grams and in the end it would be comprised of 34 individual parts and six sub-assemblies with a thinness of just 3.4mm. To put things in perspective this is nearly half the weight of the LJP prototype, it's 1 mm thinner and utilized nearly 20 less parts. Engineering is about optimizing and the team did what they set out to do to create one of the most modern and highest performing tourbillon cages of of our time.
Florian and Andi lightening the mood amongst dire times. Watch them dive into the details of the movement development.
By August of 2020 we had the first animation complete to share with the world. It of course would be modified later on as we had more internal developments to modify on the movement, but the animation was finally a first visual on what we intended to produce.
Looking at the above animation it was interesting to see that the power reserve went from 72 hours to 100 hours and today it is over 120 hours. Additional visual changes that came later on were were the ratchet wheel and balance wheel. The engineers just kept going the extra mile.
At that time we had all put everything in our lives on hold because literally everything was on the line. It was a critical point in our company where everything finally clicked. Every one of us consciously knew the ramifications that would take place if this failed and we all kicked Horage into high gear. It gives me goose bumps looking back at the forum posts and watching the above animation knowing just how close to the edge we all were. Today things are quite comfortable, but back then it was "Do or Die!".
By October 2020 we were fine tuning things even further and provided an update. As mentioned in this post the tourbillon cage today was 3.9mm, but today it's even thinner at 3.4mm. So please keep in mind that the numbers communicated earlier on changed because our team is all about reducing and chasing precision.
Tourbillon 1 like our more recent Supersede project was very much a living project that was constantly being critiqued by the team and optimized wherever possible. Parts and size reduction if done right reduces moving parts that could require earlier servicing. As well a light cage like ours increases efficiency.

In the above and below the cutouts would change again. Retaining decoration and peak performance is a delicate balance.
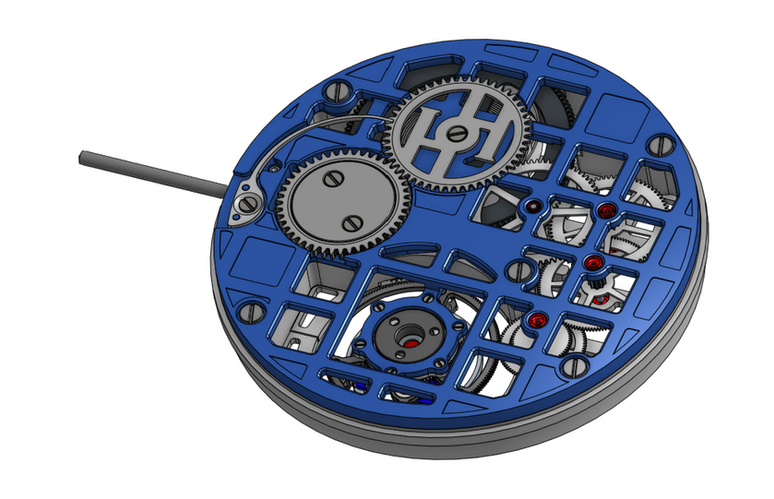
Main plate is missing some lettering in the above, but things were getting close. Check the forum post from back then here.
A major update communicated in the October 2020 forum post was the development of the screw balance wheel. It would help Lenny in regulation squeeze out the maximum accuracy potential for the tourbillon and it also looks much more visually captivating.

The titanium cage with the new screw balance wheel and in rhodium. The wheel bridge would be later modified before series production.
First Movement Assembly
In late October 2020 the first plates were being machined. This is a multi step process as machines must be programmed, then parts milled. Parts are then sanded and washed to remove burs, then decoration is applied followed by plating. During this process the engineers are measuring tolerances down to the micron to ensure everything works when put together. There is a ton of back and forth and fine tuning, but once complete the movement can start to be put together.

Engineering is where it all starts and like software it never stops.
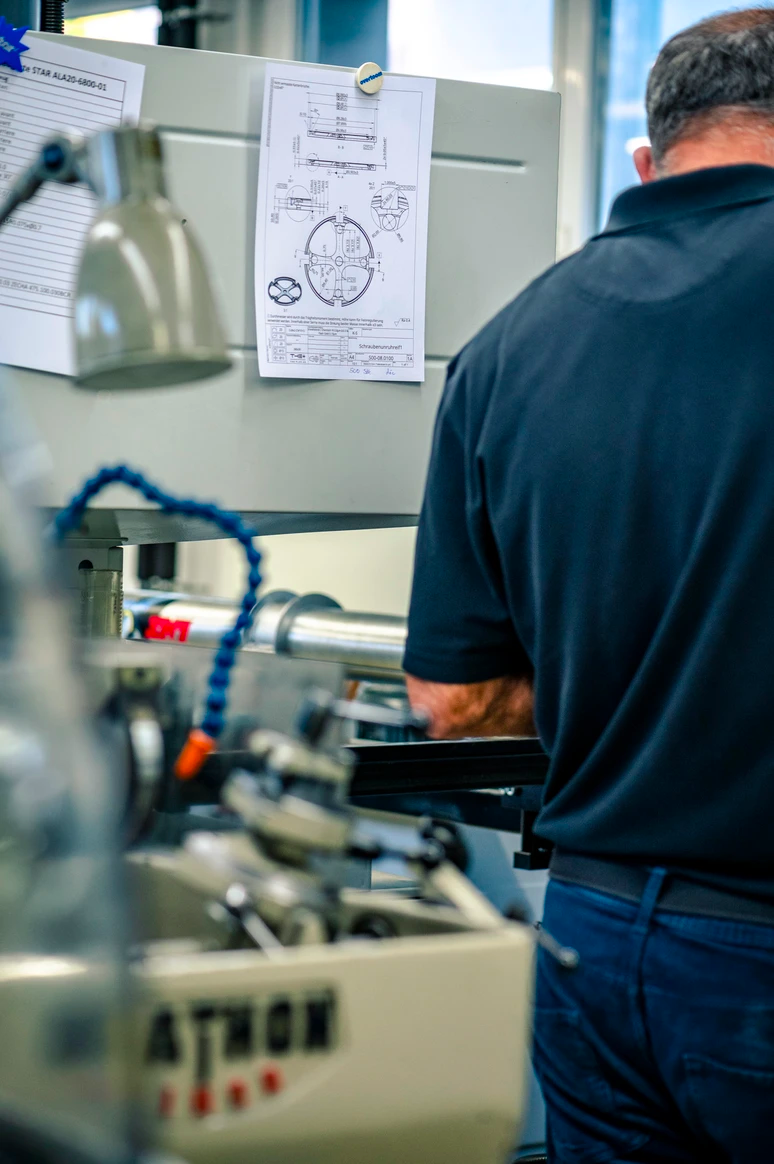
Machining the balance wheel.

Drawings for a decoration tool.
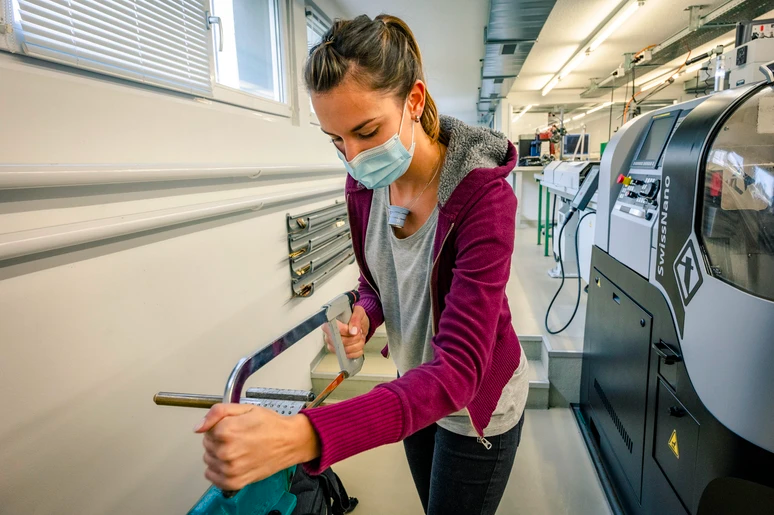
Marcella getting to work.

This is what in-house looks like. You make the parts to to make the part!

Following the machining of bridges they go out for wire cutting.
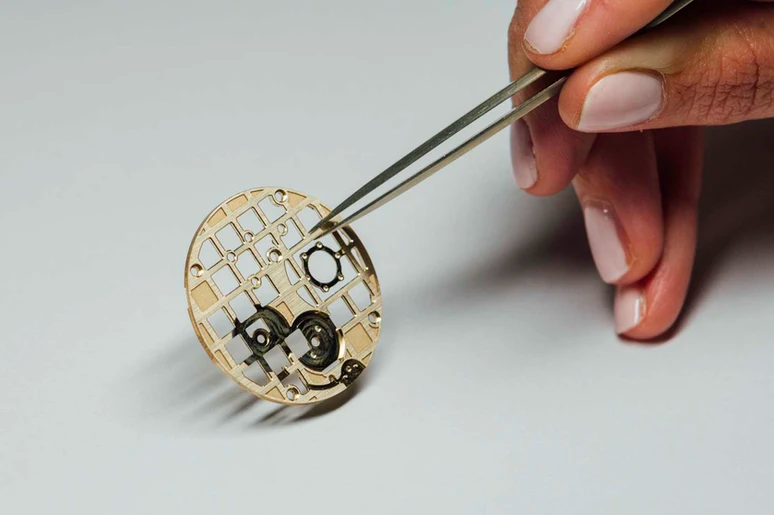
Check the forum post here
Just six months after communicating the project, in December 2020 we started to build up the first movement. Looking back at the forum post from that time you can see all the raw parts being put together.
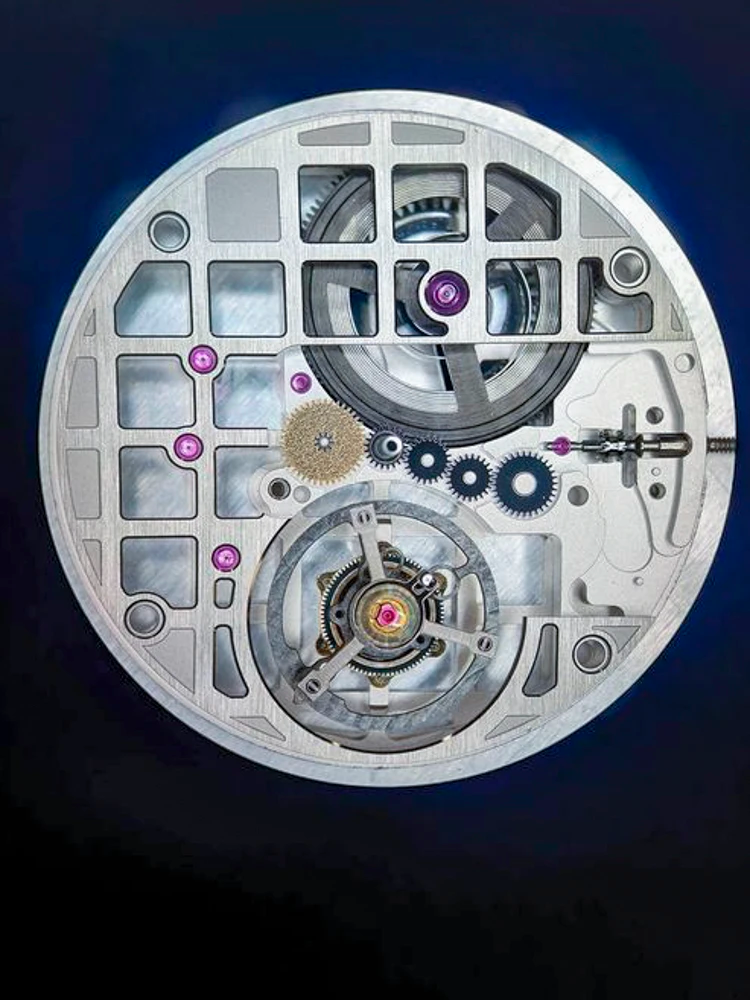
It was starting to look like a movement. Still many parts needed, but quickly it was coming together. Check the forum post here.
On December 20th, 2020 I had both the phone and a partially built tourbillon in hand and was able to snap a photo just in time for the holidays.
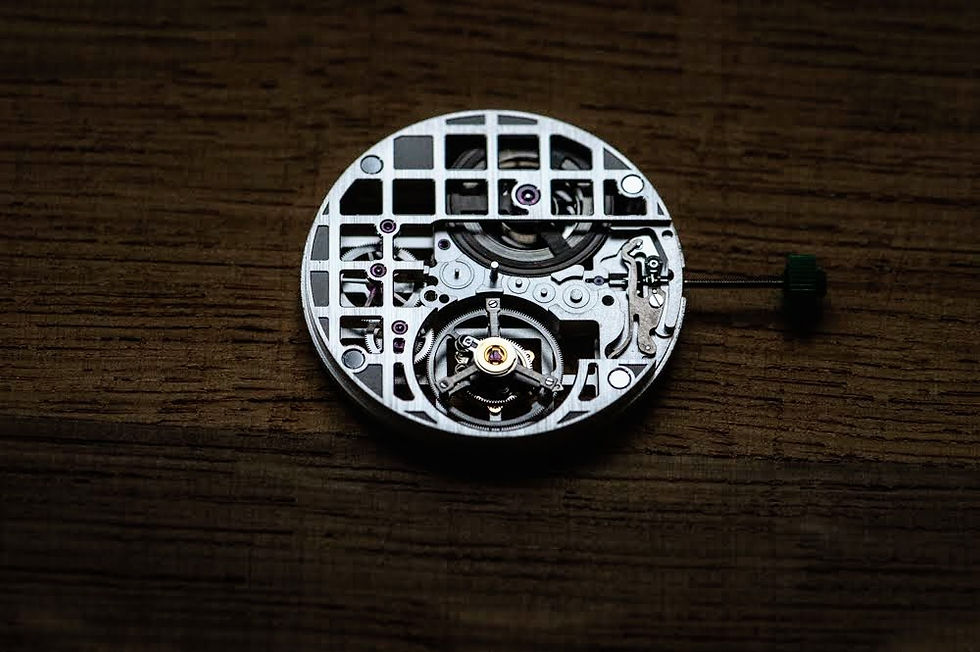

The cage is more built out and just waiting on some final parts to make it all tick.
The Excitement of Real Parts In Hand
Marcella doing the brush work on each and every movement.
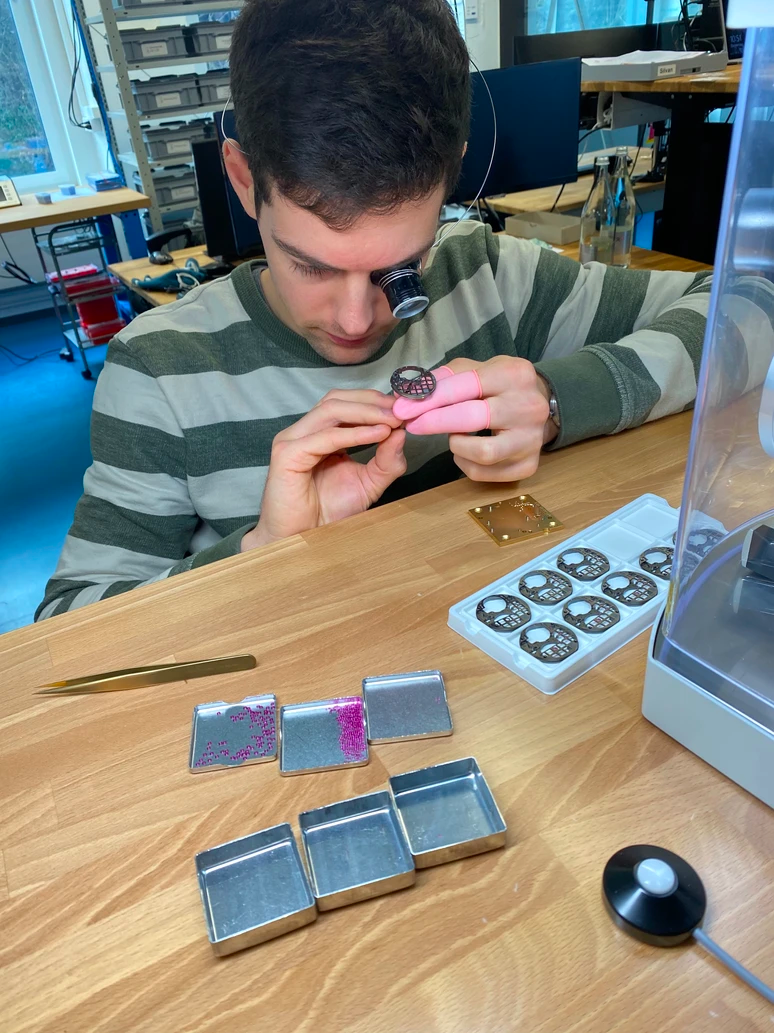
Silvan getting read to set jewels in the freshly plated main plates.
Jewel setting
Tolerances being checked to ensure absolute precision.
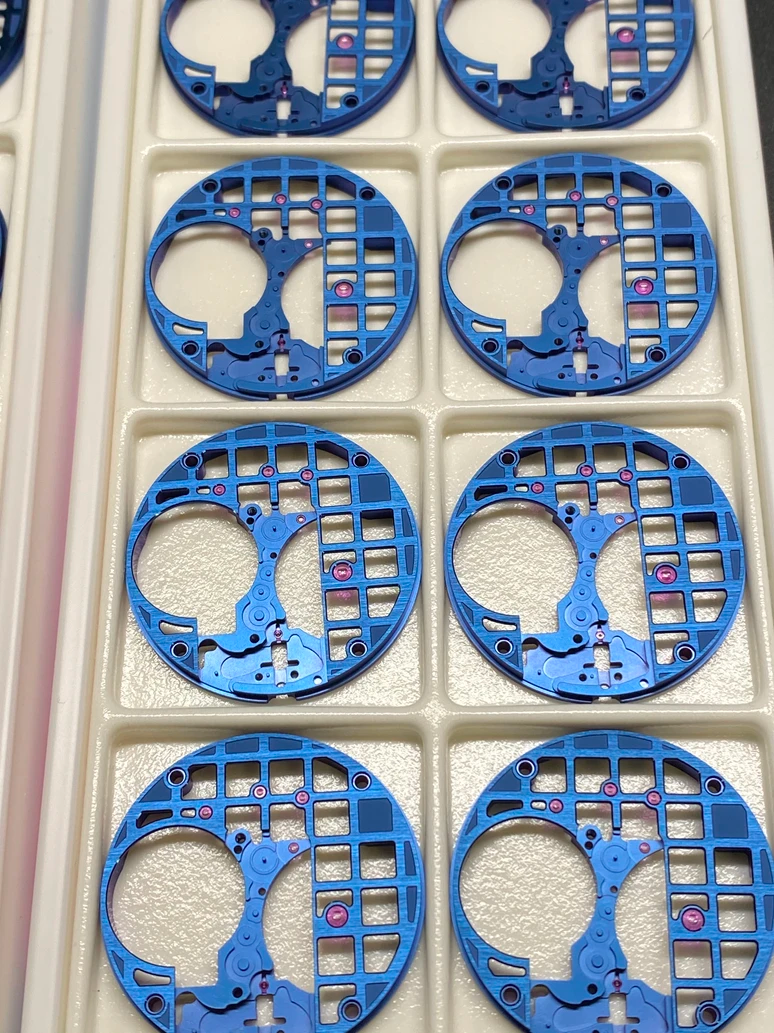
Jewel pressing is finished and ready for assembly.

An example of one of many tools we engineer and make ourselves. It's one thing to make a movement, but to make a proprietary movement you also need to engineer and produce all the tools for the parts yourself. This is the tool that holds the bridge of the tourbillon cage for jewel setting.
First Prototype Watch Complete
On January 28th, 2021 the very first tourbillon prototype watch would be assembled.

A proud Lenny having cased the first tourbillon and to be the first with it on his wrist.

A beautiful achievement. Lenny still has the rings on his finger from the finger protectors 😂
An Issue In Production
With this prototype we noticed some issues in production with the titanium parts used in the tourbillon cage. The bridge that the cage sits on needed it's part material slightly increased as Silvan was noticing some deformation of the parts when setting jewels. This would be the first delay that we would incur with production after a flawless run and on February 9th, 2021 we put together a video relaying this delay as it would impact delivery. However given that brands were still only starting to realize that the world did not end in 2020 we still were able to engineer new parts and get them machined very quickly.
Check the forum post here.
Watching the assembly of the first watches come to life was an incredible feeling both for you the customer, but also for our team. We had finally achieved what we set out to do.
Silvan assembling the tourbillon cage.
Watch Silvan assemble the tourbillon movement.
Watch Lenny build up the first Tourbillon 1.
The First Watch Delivered
Only eight months after communicating that we would make the tourbillon movement we delivered the first watch in March 2021.
A very tired Silvan with the very first Tourbillon 1 watch ready for delivery on March 26th, 2021. It's great to read the comments in the forum post and all the very nice emails received from customers and their delight with Tourbillon 1.
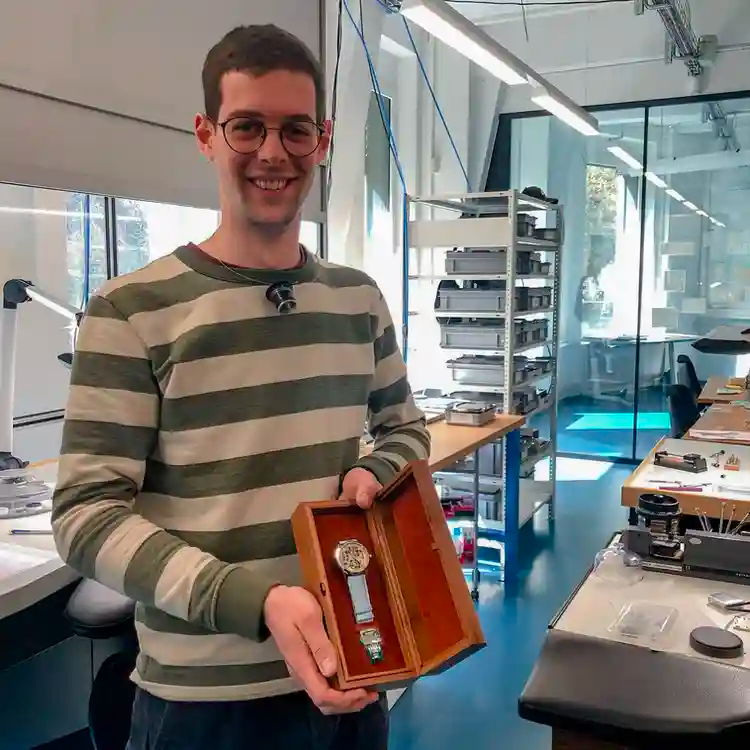
Silvan with the first Tourbillon 1 and original packaging. The packaging would change later and we will share more on that in a future post. Check the forum post here.
With the first pre-order round shipping throughout spring to early summer 2021 we wanted to take a breather, but our little brand was still relatively unknown and the cost of production had a significant impact on our bottom line. We had sold around 110 tourbillons at this point which was quite admirable, but from an accounting perspective we would need to find a way to up that number before the order deadline of August 1st 2021.
Stay tuned for the final chapter in the Tourbillon recap.
Till next time...
Landon Stirling
Great story and good experience. Looking forward to see Tourbillon 2!