The Tourbillon 1 development is going as planned and likely a little ahead of schedule.
My apologies for the delay since the last update, however we have many exciting things in the works such as a new ring Horage founder Tzuyu and watchmaker Marcella are bringing to market. You can check that out here https://www.kickstarter.com/projects/cosmocage/cosmo-cage-a-bespoke-ring-like-no-other-by-horage. We will have a separate journal post on the ring details later on.
Since my last update all I can say is that things have been moving at light speed. The most challenging part of the project for Tourbillon 1 has been finding a reliable partner to produce the titanium components that make up the flying tourbillon cage. One would think this is quite standardized since the tourbillon has been in existence for 200 years, but since we engineered this design from scratch each part is completely unique and needs to be made to order.
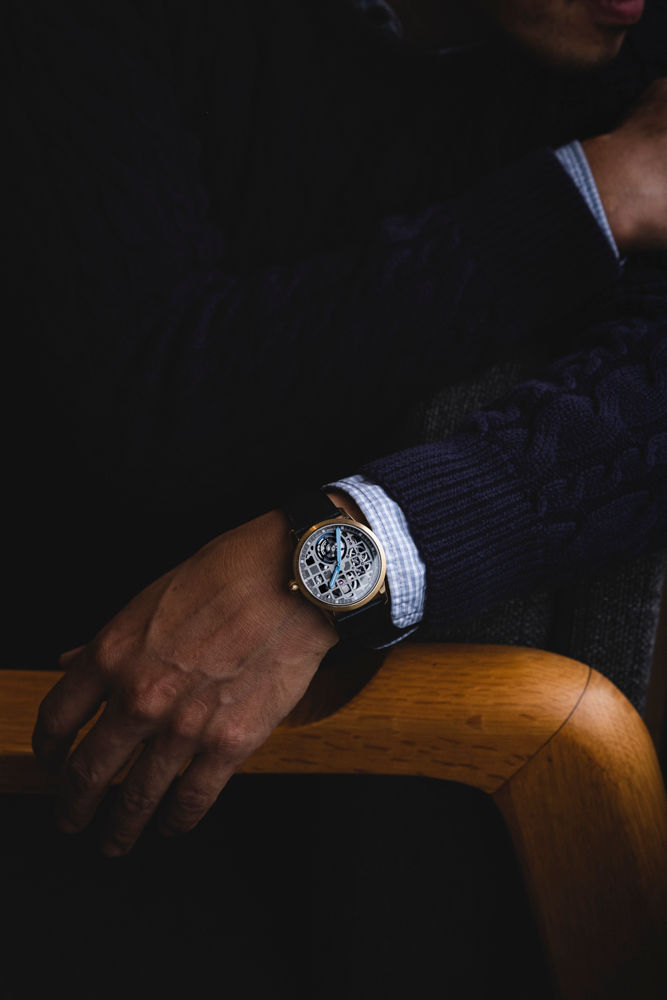
The gold case tourbillon is beautiful.
Given the restrictions around Covid-19 the team has been helping me out immensely by taking photos and video with their mobile phones.
It was with great excitement that Silvan Deutschmann the Tourbillon 1 lead posted the raw cage in a recent internal work update. Seeing things come to light in person is unbelievable and he is beginning to test the cage to ensure It meets/exceeds his calculations.
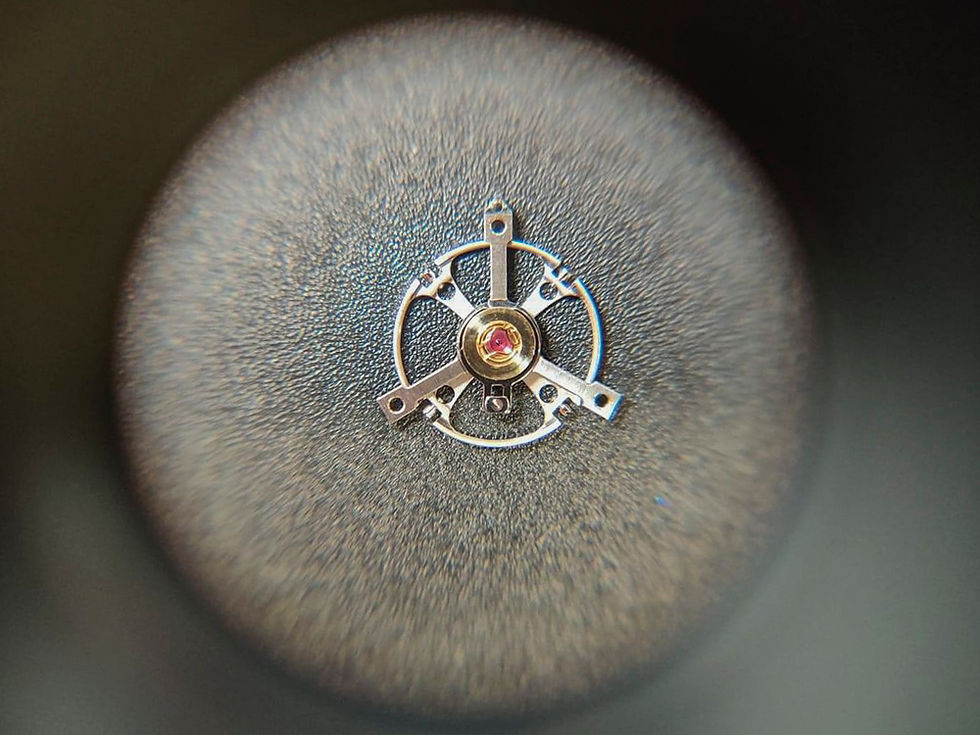

Shot through the loupe at just 0.02 grams this thing has been made to fly!. Keep in mind this is the raw build and the decoration is still needing to be applied to the materials. At the rate the project is moving it won’t be too long till you see the finely decorated cage and movement.
As you see in the above shot, the luminous indicator is not included, but we recently received those and you will see just how small they are in the image below. A good reference is to look at the fibres of the case and imagine just how magnified this needs to be.

One of the big developments with the cage was the decision to utilize a ball bearing in the cage construction. Ball bearings are far more stable than a jewel and pinion construction and this means they are the ideal solution for a truly everyday timepiece. Few utilize these in their movement construction because they are the most costly portion of a tourbillon cage.
Everything looks bigger under the microscope, however in the below you can see just how small this ball bearing is. The gear train bridge affixes the ball bearing in six positions on the backside of the movement.

In the previous update I had mentioned we had DLC coated (Diamond Like Carbon) coated main barrel. Given the Tourbillon 1 open skeleton design its important to mitigate abrasion as to avoid fragments moving around the interior of the movement. Silvan has begun testing the DLC performance and has already simulated 10 years of heavy use. The simulation re-creates situations of winding, over-winding, partial unwinding and full unwinding. You can see in the video below how this is carried out. The tests have positively concluded our expectations in performance.
In the above video you have a closer looks at the spring compression within the main barrel. Day and night this has been in motion to simulate a 10 year use case.
In the previous update we shared some of the bridge development. Since then more bridges have been placed into production and we love watching the laser work its magic cutting out the slightly inset closed squares of the movement bridges. Later the the 30 degree edges are milled with a diamond cutter.
With more bridges and components on hand to work with Silvan has also begun the raw assembly of the first movement. In conversing with Silvan he plans to build up 10 movements over this month for testing. In January 2021 we will begin production and of course in February we will begin shipment of the first pre-order round, which will have us running as planned.
Please keep in mind that decoration details are not completed and these are the raw materials.

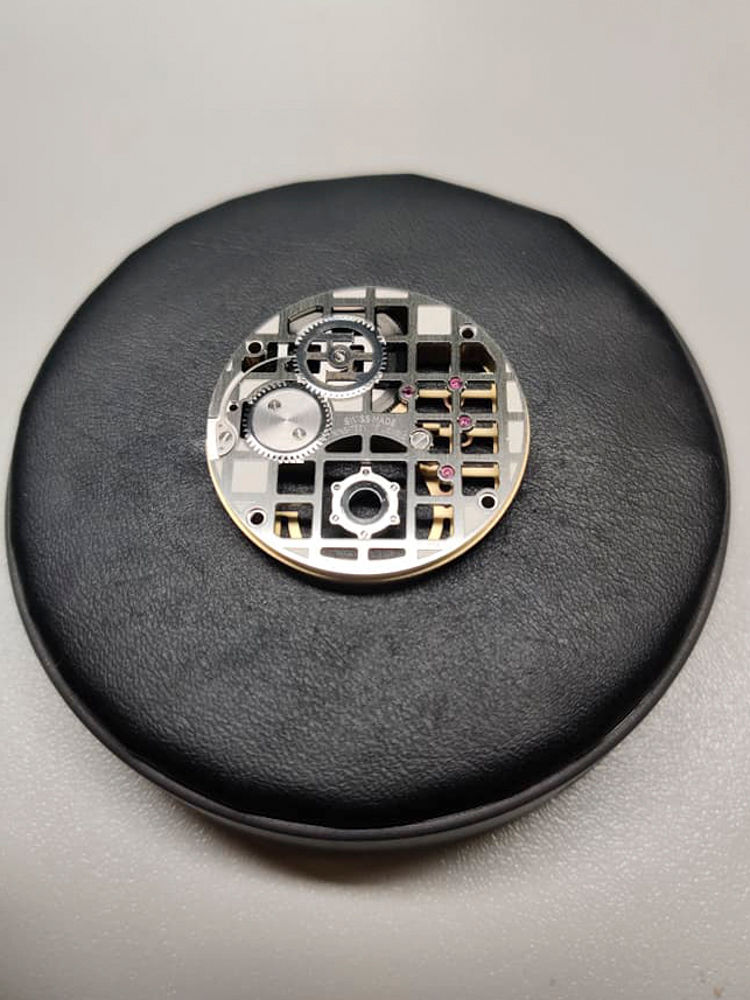

On a final note our engineering team celebrated this week the test results of our completely new in-house hands friction mechanism. Florian Serex was overseeing the calculations and when it came to test the physical mechanism it performed as calculated. The hands friction mechanism will be utilized in both the Tourbillon 1 and K2 movements.
The team has been relentless in their development of the Tourbillon 1. Every component is being tested thoroughly before it can pass our stringent quality control measures. The value of T-zero production really shines through and enables us to remain agile and confident in the final product production.
We cannot wait to share with you the first complete build of the Tourbillon 1 and look forward to the watches arriving on your wrist very soon.
It would be great to hear your comments and feedback. As always, any questions are welcome.
Till next time…
Landon Stirling
Rest assured - those who have purchased anxiously await their watch. I'm wearing my "Multiply" in honor of what's coming. For those unfamiliar with the K1 - it truly does have a significant reserve and rarely deviates by more than a few seconds a day. The only gripe as it were is that for us aging watch wearers a larger date window like Bucherer's Manero uses would be nice. Regardless, marvelous achievement that is a harbinger of the Tourbillon to come.
Very good work, both the making and the story telling around this awesome project
Really exciting to see the first parts being ready for assembly and looking forward to seeing the first assembled test watches. Congratulations to the whole team for this tremendous effort!