To live up to its name of being a true all-terrain sports watch we felt Supersede needed to have a pressure rating to match. Personally I wanted to be able to take it underwater and although I understand 100 meters is enough, I also understand there is a misconception as to what is deemed dive worthy. 200 metres is a nice big round number and is marketed as the benchmark in water resistance throughout the industry, but getting to this in a thin low profile watch isn't easy.
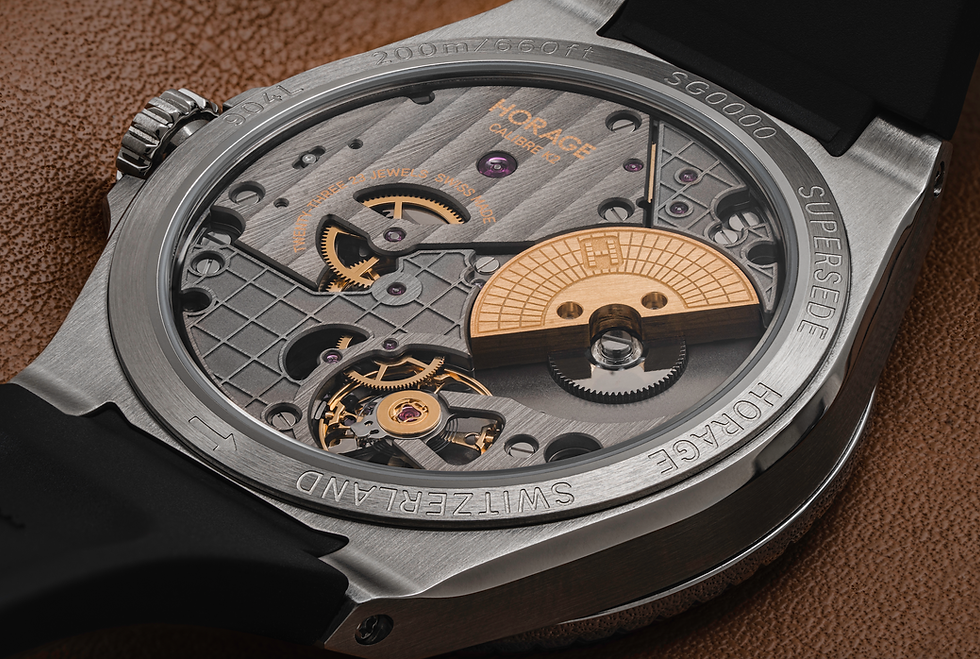
Given that Supersede is fitted with a timing bezel the community has only amplified the desire for a higher pressure rating. Increasing this is no easy feat as history shows. To our knowledge there has not been a 200 metre rated, micro-rotor GMT watch under 10mm in thickness, not to mention the addition day/night indicator, power reserve indicator and calendar. If you find one please let me know in the comments.
From the start of the K2 micro-rotor project Jonas Nydegger our head of engineering has had his eyes set on delivering the high performance K2 at just 2.9mm and the full function GMT version at 3.6mm. It's taken 5 years of engineering to achieve this and with a sound case and seal construction the next goal for Supersede would be to reach 200 metres of water resistance.

Recently Jonas, Andi, Tzuyu and myself sat down to work through the Supersede production milestones. At the top of the list was pressure rating for Supersede as Jonas and the team have been relentless in development. The internal elements of the case and seal kit have been determined and are in the current working prototypes. The next step was to test the watch and make revisions where needed. The case construction has been carefully engineered to ensure it stands the test of pressure, but our major concern has been the amount of exposed crystal which could have the biggest impact on pressure testing. During our meeting we decided the next day we would start with testing.
Did Supersede achieve 200 metres of water resistance?
Our case constructions and seal kits have always served us well up to 100 metres, but now we were headed into uncharted waters with our first ever 200m watch. Needless to say our team has been prototyping every aspect of the watch from the new K2 micro-rotor movement, to the micro-adjustment bracelet and the case.
At the start of June it was time to put Supersede to the pressure test. Our founder and the one we call the "boss" Tzuyu headed into town with three Supersede prototypes to get them tested at a partner watchmaking facility. That afternoon she called to inform me of the result.
"They passed! All of them!" She excitedly told me on the phone. Both of us were hugely relieved. Knowing her I knew she must have made a video with her phone, but in the excitement of the moment she had forgot. However the following week her and Celine went back and tested another and made a video for everyone to see.
The device used to measure the test is made by a Swiss company called Sigma Electronics SA and is the go-to standard in the Swiss watch industry. The watch is placed in the centre and then closed. The chamber is then pressurized to the desired depth rating. As pressure is applied the device measures the strain applied to the watch which is typically placed on the the Sapphire crystal. Once the maximum pressure is reached the chamber holds that pressure for a matter of time to gauge changes in the strain applied to the watch as well as to see if any air pressure changes occur such as air entering the watch. Once the time has passed air is released and pressure returns to normal. The device then provides a pass or fail indication for the watch.
For Supersede the maximum pressure was set to 200 metres and as already stated it passed the test. What we did notice is that there was a minimal amount of strain or deflection on the sapphire as this is normal and occurs under pressure. Having sapphire crystal on both the front and back of the watch made it obvious that there would be some changes in the structure, but we were pleasantly surprised just how well it performed. Typically watches going to 200 metres do not make use of sapphire on the case back because it's easier and cheaper to work with steel and achieve a high depth rating.
With the watches now tested we know 200 metres has been achieved, however as engineers we could not simply stop there. Pressure works both in a downwards and outwards direction therefore the minds at work looked to do the following.
First, it was decided to double the thickness of the o-rings on both sides of the sapphire crystal. These o-rings create a seal between the sapphire and the 904L stainless steel case and case back. As pressure is applied the crystal gets pressed down and this causes it to push outwards to the side of the case. Doubling the o-ring increases material which helps mitigate compression outwards against steel. In addition there is a seal between the case back ring and the case.

The second part we looked at optimizing is the crystal itself. We have decided to increase the inner curvature of the crystal. This change allows for more space between the hands on the dial side and movement on the case back size. As you can see in the above image there is increased space between the hands and crystal. Combined with the increase in o-ring size the Supersede looks to be ready for some time underwater.
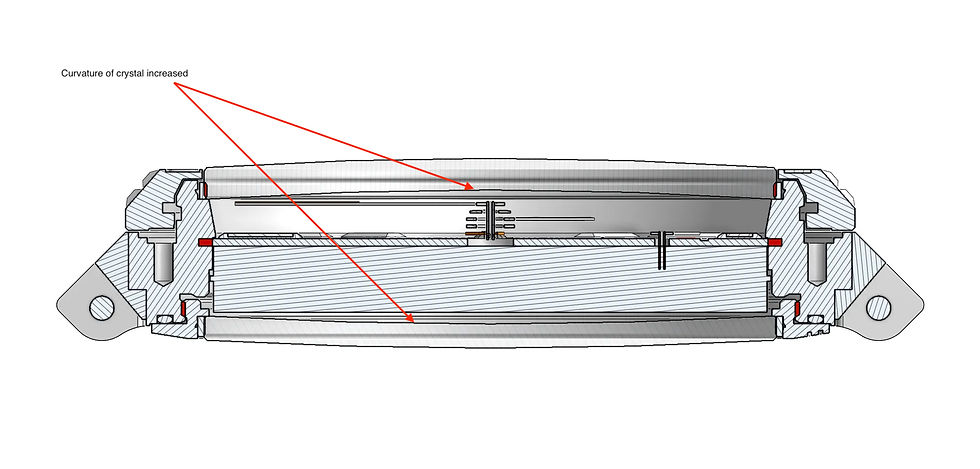
It's a great relief that we can keep the 200 metre designation and will be able to deliver as we had hoped to the community.
Whats Next?

The final piece of the puzzle is rotor material and we look to deliver an update to you in the coming two weeks. At some point next week we will receive the rotors from our supplier just down the road.
Let me know your thoughts in the comments.
Till next time...
Landon Stirling
This is great news Landon but it was never in doubt that the watch could reach 200m 😉
Did you guys ever think to go further to say 300m given how well it performed to 200m? I think with the changes it is worth a try, don't you think?